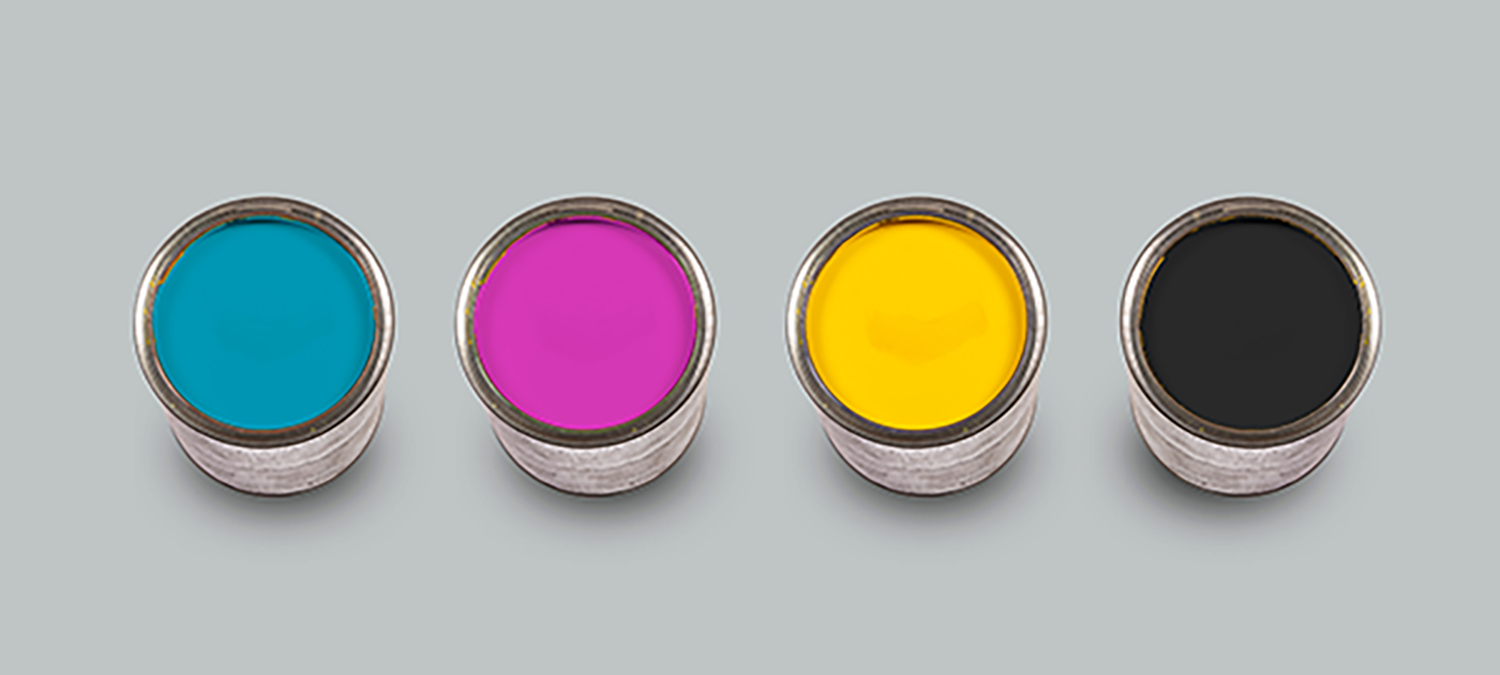
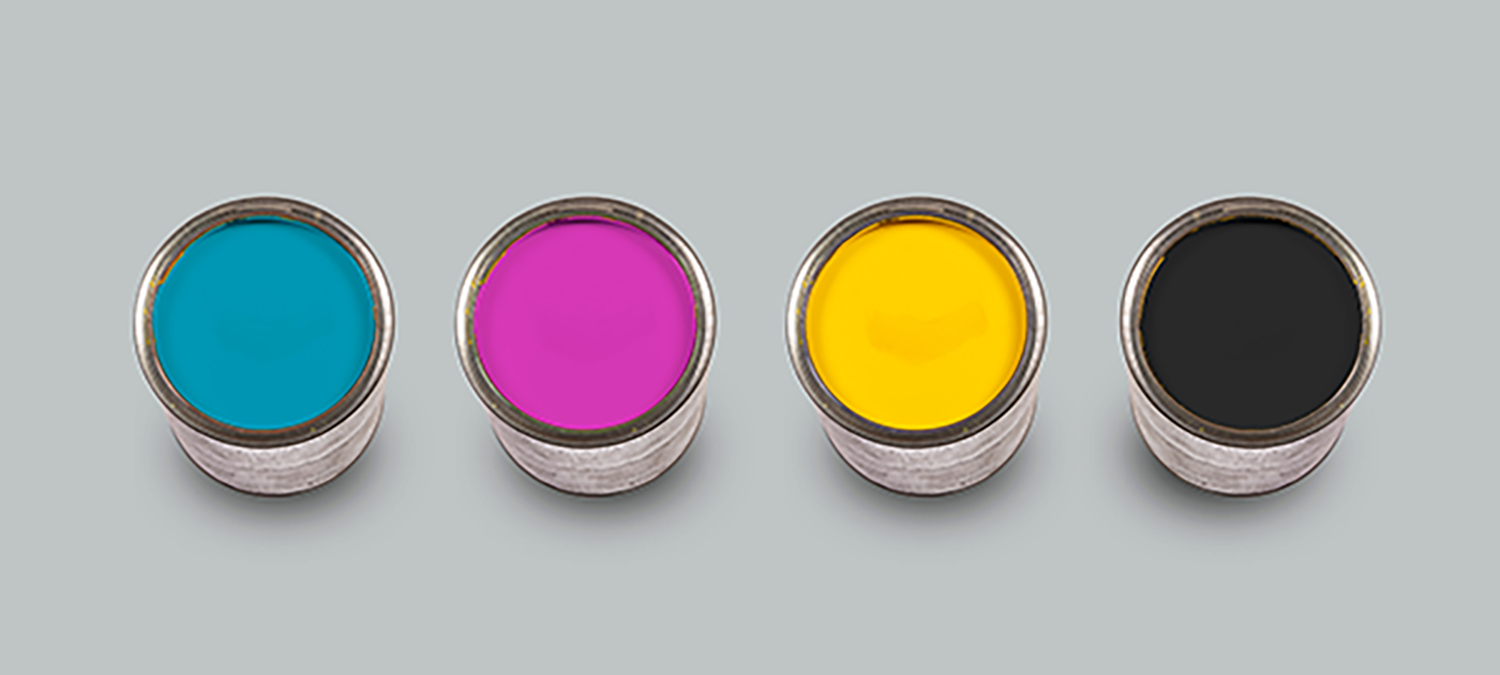
Have you seen any of our social media posts featuring custom printed glass jars? For about a year and a half now, we have partnered with the Crazy Mason Milkshake Bar to produce bright, fun, and colorfully printed mason jars. The Crazy Mason is the perfect stop for all sweet tooth lovers with all kinds of milkshakes loaded with "crazy" toppings (a slice of cake, a donut, or a whole cookie to name a few.) However, no Crazy Mason milkshake is complete without it's unique jar. In this blog post, we'll dive into how exactly we screen print these jars.
Four-color process screen printing, also known as CMYK printing, is a method used to achieve full-color prints by combining four primary ink colors: Cyan (C), Magenta (M), Yellow (Y), and Key (K) or Black. This printing process is commonly used in various industries, including graphic design, advertising, and apparel manufacturing. Here's how it works:
-
Color Separation: The first step in the four-color process is to break down the full-color image, in this case the jar design, into its four primary color components: cyan, magenta, yellow, and black. This is done using specialized software or image processing techniques. Each color component will be printed on a separate screen, with a halftone pattern (tiny dots) to simulate the different shades of the color.
-
Screen Preparation: Once the color separation is complete, a screen is prepared for each color component. These screens are usually made of a fine mesh material (e.g., silk or polyester) stretched over a frame. The screen is coated with a light-sensitive emulsion.
-
Film Transfers: Each color separation is printed onto a transparent film with opaque black ink. These films act as stencils for each color. One film is created for each color: cyan, magenta, yellow, and black.
-
Exposure and Washout: The films are placed on top of the corresponding screens, and the screens are exposed to a bright light. The light hardens the emulsion except where the opaque areas of the film block it. After exposure, the screens are washed out with water, leaving open areas where the ink will pass through during printing.
- Color Alignment: Achieving accurate color registration is crucial to ensure that all colors align correctly. Slight misalignments can lead to color fringing or other unwanted effects. Modern printing equipment often includes registration systems to help with precise alignment.
-
Printing Process: The printing process begins with the lightest color, typically yellow. However, since the glass is transparent, we first print a base coat of white ink so that each color applied on top is fully opaque. The screens for each color are set up on the printing press and the corresponding ink color is poured on top of its own screen. A squeegee is then used to push the ink through the open areas of the screen and onto the jar.
-
Overprinting: As each color is applied, they blend together to create a wide range of colors. For example, when cyan and yellow inks overlap, they create green. Similarly, magenta and yellow inks create red, cyan and magenta inks create blue, and all three primary colors combined create black. The black (K) color is used to enhance contrast and add depth to the final image.
-
Drying: After all colors are applied, the printed material must be allowed to dry thoroughly before additional layers or finishes are applied.
By repeating the process with each color and carefully aligning the prints, the four-color process screen printing method can produce full-color images with a wide range of tones and shades. This process is commonly used for printing photographs, illustrations, and complex graphics on various surfaces, including paper, cardboard, fabric, plastics, and even crazy mason jars!